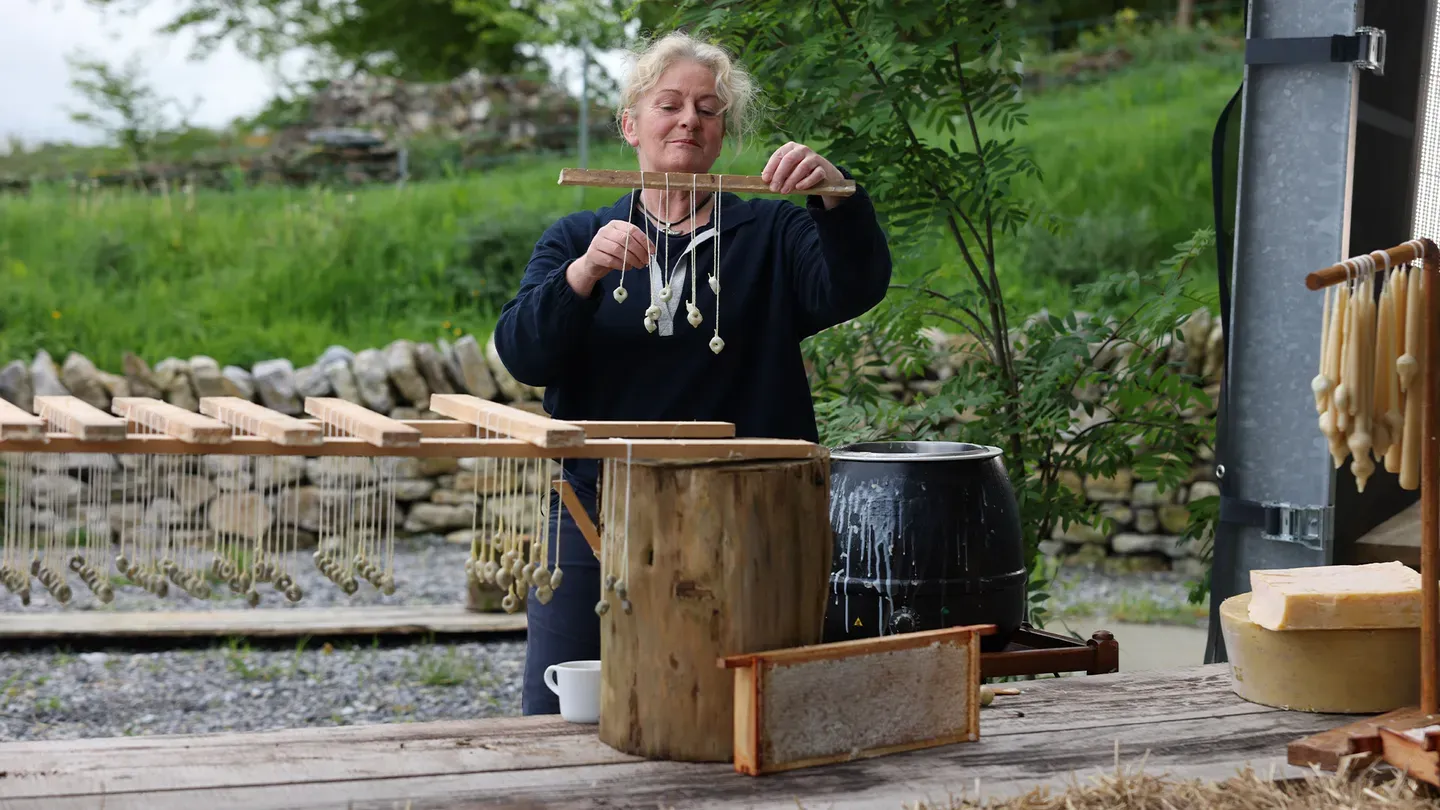
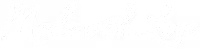
Ireland Made With Love
Special | 58m 1sVideo has Closed Captions
Explore Irish craftmanship and the skill, love and pride that go into legendary products.
Explore the legacy of traditional Irish craftsmanship through the skill, pride and love that go into legendary Irish products. From the spectacular cliffs on the Atlantic coast to the medieval castles and historic villages, Ireland’s epic landscape and rich culture are gloriously showcased.
Problems playing video? | Closed Captioning Feedback
Problems playing video? | Closed Captioning Feedback
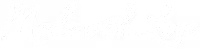
Ireland Made With Love
Special | 58m 1sVideo has Closed Captions
Explore the legacy of traditional Irish craftsmanship through the skill, pride and love that go into legendary Irish products. From the spectacular cliffs on the Atlantic coast to the medieval castles and historic villages, Ireland’s epic landscape and rich culture are gloriously showcased.
Problems playing video? | Closed Captioning Feedback
How to Watch Made With Love
Made With Love is available to stream on pbs.org and the free PBS App, available on iPhone, Apple TV, Android TV, Android smartphones, Amazon Fire TV, Amazon Fire Tablet, Roku, Samsung Smart TV, and Vizio.
Buy Now
Narrator: Ireland--it's a land of mythic beauty, from kelly-green pastures to sparkling Celtic coastlines.
These natural wonders have fed the muses of Irish artists for generations... and today, they still spark this nation's most fertile imaginations.
Man, voice-over: Well, I think the landscape speaks for itself.
It's a very beautiful place.
Woman: There's absolutely no shortage of inspiration.
Man 2: It's a great place if you are creative because you have everything around you to look at.
Narrator: While the land itself may offer the raw material these artists need... Woman 2: I fell in love straight away, with an oyster farmer and oysters.
[Both laugh] Narrator: It's the epic history and mythic romance of this Emerald Isle that nourishes their creative souls.
Woman 3, voice-over: It's a labor of love.
Really, I love my job.
I'm so lucky.
Heh!
Woman 4: If we cease doing what we are doing, we lose a key part of Irish culture.
Narrator: That sense of shared tradition and a unique vision inspires work that's both as Irish as St. Patrick's Day and celebrated all over the world.
♪ Narrator: Across this island nation, there are close ties between where people live and what they create.
Nowhere is that more true than in the county of Kilkenny, which sits along the banks of the River Barrow.
It's the longest of Ireland's 3 sister rivers and winds through towns that trace their roots to medieval times, including the town of Graiguenamanagh.
Woman 4: It's a beautiful, kind of hidden, secret town.
The name itself, Graiguenamanagh, in Irish, it's Graig na Manach, which translates to "village of the monks."
Monks established the town here in 1204.
The monks, they were very religious people, but they were also very industrious.
Narrator: Cistercian monks chose this spot for its proximity to the river.
It gave them a steady water supply and the ability to trade goods with the rest of Europe.
Miriam: Ireland was known for its high-quality fleece and wool, so that was a big commodity at the time.
Narrator: Centuries later, wool and weaving are still an integral part of the local culture.
Miriam: I'm Miriam Cushen.
My name is Philip Cushen.
I'm a woolen manufacturer... From Graiguenamanagh, Ireland.
I am with my dad, the current custodian of our family business here in Graiguenamanagh.
So it's a woolen mill, and we make beautiful blankets, throws from lovely natural yarns.
Our family traces back to 1778, so I'm sixth generation of the family, but I'm the first woman at the helm.
Dad has been working in the mill since he was 16.
He took over from his father.
So Dad is still working with us, doing what he loves.
Narrator: Today, their textile mill sits on the same site where the monks had a mill and relies on the same water source... [Birds chirp] among the cleanest in Ireland.
Philip: It's ideal for dyeing.
We can get colors that most people have difficulty in getting because the quality of the water is so good.
Miriam: It's a very special part of what it is that we do.
Narrator: Their blankets start with wool from local Galway sheep, the only breed of native Irish sheep.
Miriam: We're working with amazing partner farmers that breed them, and we get to know them all very personally, visiting their farms, meeting their sheep, and collecting the fleece.
Narrator: Once the wool reaches the mill, it's hand-sorted and dyed into 13 colors.
These colors are then blended to create a range of different shades.
Miriam: So we dye it into really vibrant green, red, yellow, purple, black, and essentially that becomes our painting palette.
Narrator: The wool fibers are then put through the carding machine, where they're combed and aligned.
From there, the wool is spun into yarn at the "spinning mule," a vintage machine that pulls and twists the fibers to make them stronger.
[Clanking] This mule was built in 1890.
Philip: The mule is the oldest machine that we have.
My grandfather bought it from a mill which was closing down.
Miriam: It's a very mechanical, beautiful machine, and it's one of the last of its kind in Ireland.
When people see it, they think it's a museum piece, but it's not.
It's fully operational.
Narrator: Philip watches closely, correcting any mistakes as the mule spins and wraps the wool into yarn.
Philip: If you don't look after the little things, they become big problems, and if you don't deal with it, it will come back to haunt you.
Miriam: I love seeing and learning from my father, seeing the love that he has for what he does.
Narrator: Next comes warping.
The yarn is wound onto a large wheel, then wrapped around a warping beam.
This creates the blanket's vertical threads.
Miriam: I actually run that process.
That's one of the first stages of actually bringing it to life.
Narrator: After warping comes weaving.
Strands of wool are threaded in horizontally to finish off the fabric and make it stronger, then the newly created textile goes to the workroom, where it's carefully checked and mended to ensure the highest quality.
Miriam, voice-over: So we check for any flaws, any knots, mending all of that out.
Narrator: Over the next 4 days, the blanket goes through a finishing process that makes the fabric softer and stronger.
Miriam: And then eventually, it comes back up to the workroom, and that's where we hand-cut, hand-finish, do more quality checks.
Narrator: It can take up to 6 weeks to make a blanket, from initial design to final product, but there's no way to measure all the love and care that goes into each one.
Miriam, voice-over: For us, we've only a team of 10 here, but every member of the team touches that blanket numerous times in its journey.
So, if you have thought about it and love it yourself, then other people will see the love and the passion in what you've made.
Philip: I've always had a passion for it.
I like the machine.
I like the designing, as well.
Miriam: If we cease doing what we're doing, we lose a key part of Irish culture.
We're really passionate about sustaining those skills, sustaining that heritage.
♪ Narrator: Here in Kilkenny, few things stir passions like watching the local team play Ireland's native sport, hurling.
[Stadium announcer shouts indistinctly] Narrator: This fast-paced game looks like a mix of baseball and lacrosse.
Announcer: Here comes another goal!
Brilliant, Kilkenny!
Narrator: For some, it's more than a sport.
It's a way of life.
It's our religion, isn't it?
It's the be all and end all in the place, yeah.
Yes, everything happens in a hurling match.
Narrator: Played with a ball, or sliotar, and a wooden stick with a wide oval end, called a hurl, the sport of hurling dates back some 3,000 years.
It's the oldest and fastest field sport in the world and as popular as ever in Ireland today.
Announcer: And a cranking shot!
Narrator: For brothers David and Stephen Dowling, their love of hurling and the art of making traditional wooden hurls by hand has been part of their family for 4 generations.
David: Our great-grandfather made hurls back in the early 1900s.
Narrator: Relatives on both sides of the family played here in Kilkenny, so you might say the sport is in their DNA.
It's literally-- it's kind of in your blood.
Narrator: The brothers now run a company started by their grandfather, one that makes high-quality hurls by hand.
[Scraping] Today, they're making a hurl for T.J. Reid, one of Ireland's top players and star of their home team of Kilkenny.
Stephen: T.J. Reid is probably one of the greatest hurlers in Ireland at the moment and, uh, probably one of Kilkenny's best ever as well.
Narrator: Like every hurl they produce, this one will be custom-made, according to the shape and weight that best suits the player.
The first step is choosing the right plank of Irish ash.
If you can imagine an ash tree standing in a-- in a forest or in a wood, we're looking for the root of the ash tree.
You're looking for this turn, so the shape of your hurl will match that.
Narrator: David selects a plank of ash with the curve at the "bas," or head, of the hurl.
♪ Next, he uses a template to trace the shape of the hurl best-suited for T.J. Reid.
David: It's the type of hurl he wants, it's the shape, so what I'm doing is I'm marking that onto a piece of ash.
He likes it without any flexibility.
A "stiff hurl" is what we call it.
Thank you.
There it is.
All right.
Narrator: From there, their uncle Brian cuts the basic shape, making sure the arm remains perfectly straight... and checking for any flaws in the ash.
David: You could saw the hurl out, and there could end up being maybe a knot in it or something like that, so it should be a weak point.
Something like that, you could start from scratch again, really, yeah.
Narrator: The hurl is then turned on a lathe to give the handle its rounded shape.
At the heart of every handmade hurl is the process known as "spokeshaving."
Using a hand plane, the brothers make careful adjustments to each part of the hurl-- shaving, straightening, sanding, and smoothing-- until they get it just right, the same techniques and tools used by their great-grandfather back in the early 1900s.
David: I'm doing it, you know, 20 years now, so you kind of run on autopilot a little bit.
But at the start, doing this, you'd be, yeah, you'd be kinda shaking a bit, yeah.
Heh heh!
Yeah.
Narrator: Steel bands added to the rounded end or "bas" of the stick give it extra strength.
Stephen, voice-over: T.J. likes his own shape and two bands on it and everything, so hopefully he likes it now--heh!--- but I think it should do him.
Narrator: And the Star Hurley stamp, the mark of one of the only places in Ireland that still makes hurls by hand.
For the brothers and the community, it's an enormous sense of pride.
David: You know, you're at matches and you're watching matches on TV, and he's using your hurl, you know.
It's great.
There's satisfaction in that.
That kind of thing, that'll make you very happy, making that kind of stuff, yeah.
♪ Narrator: County Waterford.
This one-time Viking outpost has often found itself on the leading edge of Irish culture.
It's home to Ireland's first city, the first place to fly the Irish tricolor flag, and the first to celebrate St. Patrick's Day in Ireland.
It's also the home of Ireland's world-renowned hand-cut crystal.
The glass-cutting tradition here dates back to the 18th century, and for good reason.
Man: It's a beautiful area to live in.
We have the sea, we have the mountains, we have everything on our doorstep.
It's a great place if you are creative because you have everything around you to look at.
Is mise Eamonn Terry, máistir gearrthóir gloine.
Augus Cearbhall Terry, gearrthóir gloine.
Narrator: From his family-run workshop in the Waterford town of An Rinn, master glass cutter Eamonn Terry and his son, Cearbhall, create breathtaking crystal pieces.
Eamonn: What we are trying to do is tell a story with each design that we make on the piece of crystal.
So we use our language, our landscape, our history, and incorporate those into new designs.
I like doing things with my hands, and there's a great sense of satisfaction in creating something.
Narrator: Eamonn's passion for glass work started 50 years ago, when he became a glass cutter at the world-famous Waterford Crystal.
It took another 10 years of training, apprenticeships, and exams before Eamonn earned the title of "master glass cutter."
Eamonn: This is the bowl that I qualified on to become a glass cutter.
You were examined on this bowl by your peers.
If I wasn't able to do this, I wouldn't be able to create all the other things that I have.
That's a precious piece of, uh, glass, or crystal.
Narrator: Now, Eamonn is one of only a few artisans left in Ireland who still cut glass in the traditional way.
Eamonn: You probably could count them on your two hands.
Narrator: Today, he's making a crystal decanter with a modern design inspired by the letters of Ogham, an ancient Irish alphabet.
He marks the glass with the vertical lines that will guide him as he makes each cut.
Eamonn: I do more traditional-type cutting, but I also do the more contemporary-type glass now.
Narrator: At the cutting station, he uses a diamond-coated wheel to help him make smooth, precise cuts.
Eamonn: In my armory, I would have over 200 different wheels for doing different cuts on different pieces of crystal.
If you pick the wrong wheel, you're going to make a mess of the glass.
Narrator: Just as important as the wheel is the deftness of his hands.
Eamonn: It's fairly tricky cutting into a bottle like this.
I have to be very careful that I don't make the cuts too heavy or too light.
That only comes with experience.
You get the feel of what you're doing.
That's the hard part.
Narrator: Water cools the crystal to keep it from overheating and breaking.
Eamonn: We're nearly halfway around the decanter already.
My favorite part is on the cutting wheel, actually creating.
If I've made up a design, to see how it goes from the very start to the finish, and then, when I have the finished product, to see what I've achieved, there's a great sense of satisfaction.
Yeah, very happy with it.
Yup, that's ready now.
All it needs then is a good whiskey.
Heh!
Crystal is meant to be used.
Think now, the younger generation are falling in love with crystal again.
I don't consider it a job.
I would work every day because I love what I do.
Narrator: A love of crystal and a cherished Irish tradition Eamonn is passing to the next generation.
Cearbhall, voice-over: I think I was 12 years old when I cut my first piece of glass, and he gave me the apprentice entrance exam, so I'm well-trained in at this stage.
It's nice that if you create something, that it just doesn't stop with you when you are finished.
I would hope that what we've built up over the last number of years will continue.
Narrator: In northeastern Ireland lies the gentle county of Monaghan, known for its little hills, or, as we Irish call them, "drumlins."
Woman: It's Drumlin County, and it's always kind of likened to a basket of eggs.
They say it makes you curious, you know, what's over that hill?
[Laughing] Another hill, so, kind of makes curious people.
Man: We always have this saying that there was too much land in Monaghan, so they stacked it high.
I'm Seamus McMahon.
I'm a craft brewer from County Monaghan here in Ireland.
Narrator: Seamus grew up on this dairy farm, one of many that dot the agricultural region.
Seamus: My father inherited the farm from his father, who inherited from his father, so we're probably 10th-generation McMahons here.
Narrator: While drinking a craft beer for the first time with his wife Siobhan, he decided to expand the dairy farm and open a brewery.
They named their brewhouse for the medieval "Brehon Laws" that once ruled Ireland and allowed every clan to brew beer for their own family.
♪ Seamus and the team brew everything from stouts and lagers to IPAs.
Today, they're making a traditional Irish red ale called Killanny Red, named for the parish that surrounds the farm.
The process starts with crushed barley that's loaded into the hopper.
Seamus: We use barley, we use water, we use yeast, and we use a lot of time, and they're the 4 ingredients that microbreweries use.
Narrator: It's how these 4 ingredients are combined and treated that makes each of their beers unique.
The barley mixes with the water in the mash tun.
This process extracts the sugar, which is called "wort."
It is then transferred to a copper kettle for boiling.
Seamus, voice-over: And then we add the hops.
So the hops give you preservation and give you flavor.
Narrator: Once the beer is cooled and reaches the fermenter, yeast eats the sugar and converts it into alcohol.
And I suppose the magic ingredient then is time.
It's a slow process, but produced in a sustainable way.
We don't use any artificial flavors or preservatives.
We just use a lot of craft and time.
Narrator: The entire brewing process-- barley to beer-- can take up to 6 weeks.
Any extra barley, they feed to the dairy cows.
They even bottle their beer on site.
Seamus and Siobhan hope their love of craft-brewing will lead to a new family tradition.
Seamus: She has just recently got engaged to Jim.
In a roundabout way, we've dragged a brewer back to the farm, yeah.
I can do it all from the stone's throw from my house.
You know, you still have time for your family.
Have a cup of tea any time of the day, you can have a drink any time of the night.
It's quite relaxing.
It's quite an easy team.
It's how good beer should be made, I think.
[Birds chirp] Narrator: The quaint market towns of County Monaghan are home to a growing community of artisans.
They carry on age-old traditions and make the most of what the land has to offer.
I'm Brenda McGinn, and I'm a ceramicist from Monaghan, Ireland.
Narrator: From her studio in the 19th-century mill village of Glaslough, Brenda spends most of her days creating ceramic pieces that she sells in her shop, passing along her love of the craft.
Brenda: I think it's in us all to create, you know?
It's just a little bit of discipline.
Every person who makes something, they are actually making part of themselves, and it's magic.
Narrator: Brenda grew up in a family of academics and broke the mold when she wanted to study art.
She started as a painter at Ulster University in Belfast, then switched to ceramics by year two.
Brenda: The first day I went in, it was just, like, clay everywhere, kind of just grew on me.
Narrator: Pottery soon became her passion and her career.
It has challenged her to be both artistic and practical.
Brenda: No fuss, like our ancestors.
They needed the clay to do a certain job.
It didn't have to be fancy, it was just what it was, and that's kind of where I'm coming from.
I like the simplicity of it.
Narrator: Pottery in Ireland dates back over 6,000 years, but it wasn't until the 13th century that Anglo-Normans first brought over the potter's wheel.
The process and materials haven't changed much over time.
Brenda is always on the lookout for local ingredients, from the organic clay to the powder for the glaze to the hand-picked plants she uses for decoration.
She draws her inspiration from the serenity of the land.
Brenda: When I'm doing the decoration and the painting, I'll just take a whole day.
I'll go into my studio and close the door, and I don't play music and it's just quiet, and that's me in my happy place.
It's just a love affair.
It's like an indulgence.
I swear, I--I feel like there's someone giving me a chance to do all this is just a miracle.
Narrator: A love of the craft, and of clay, that might just live in each of us.
Brenda: So Patrick Kavanagh's a famous poet from Monaghan, and one of the lines in his poem is, "We are all creatures made of clay."
So I just think, yeah, clay is definitely in our DNA.
There is just a resonance that I feel when I'm in a restaurant, and it's a handmade something... and the bread is on something full of history.
You can actually feel it.
♪ Narrator: Just up the road is Castle Leslie Estate.
It's one of the last Irish castles still owned by its original family.
Over the years, this 17th-century palace has lured politicians and poets to relax and unwind.
The other reason people come here is the food.
Today, Aaron Duffy is preparing a gin-cured sea trout dish that relies on local ingredients.
Aaron: We use it for different dishes, and that just works beautifully with the light, delicate flavors of the sea trout and the mackerel.
To add that smokey flavor, we're going to just torch the skin ever so slightly, and you'll see it starting to rise.
That'll just firm up the textures of it.
Ireland is, yes, a small country in some aspects, but there are so many different producers.
We use as many local producers as we can.
Narrator: Pickled mackerel and sea vegetables from the Irish coast, herbs and flowers from their gardens, and the final touches-- avocado purée and oil infused with their own garlic.
♪ Aaron: It's all about letting everything speak for itself on the plate.
Everything's just nicely balanced and spread out.
Narrator: A culinary feast that tastes even better on one of Brenda McGinn's handmade plates.
Foodies find a lot to savor in Ireland.
While many are drawn to traditional recipes, there are plenty of choices on the menu that mix the old and the new.
A popular ingredient in modern dishes is Irish goat cheese, which can add a taste as varied and unique as the farms that create it.
Mohamad Ait Hammad: It's fun when you know that you're going to have something tasty at the end.
Heh heh!
You can't wait to eat.
Narrator: Ireland is known for its stouts, but bartenders are also trying a hand at modern drinks, like the basil smash-- millennial take on a classic cocktail.
Man: It's a gin sour, shaked with fresh basil leaves.
[Ice rattling] What's important in life, it's eating, drinking, and sleeping.
If you can create a nice drink or nice food after they had a hard working day, it's just beautiful.
Narrator: While there's room for innovation, the traditional Irish toast, "sláinte," is still in vogue.
It means "good health."
[Birds chirping] Narrator: It's the soundtrack of the Irish soul... an enchanting melody that evokes the stunning landscape of this Emerald Isle.
[Harp playing] The harp is Ireland's national symbol.
You can find its likeness on everything, from Irish currency to an iconic brand of beer.
Here in County Galway, on Ireland's western seaboard, Natalie Surina uses skill, patience, and an artistic eye to recreate traditional Irish harps.
I'm Natalie.
I'm a harp maker from Galway.
Narrator: The earliest Irish harp was made more than 7 centuries ago.
Back then, Irish harps were played all over, but by the 18th century, they had fallen out of favor, and making them was a dying art.
I think there was so much knowledge which is forgotten, and there is so much experience which is forgotten.
Narrator: Natalie fell in love with the classic harp while doing research for her Ph.D. in Irish studies.
There was just one problem.
Natalie: I couldn't afford it, basically.
[Chuckling] It was so expensive, so I thought I'd make a harp for myself.
Narrator: Since then, she's dedicated her life to making her own harps, copies of those that survive from centuries ago.
Natalie: I like to replicate, 'cause it gives me an idea of how things were done back then.
Narrator: It takes an entire year to make a harp, as Natalie slowly turns huge pieces of local Irish willow into an elegant instrument.
First, she marks the outline for the 3 key pieces of the harp: the soundbox, the pillar, and the harmonic curve, or neck.
It's the same basic blueprint harp makers relied on centuries ago.
Natalie: Very little is known, actually, about these instruments, why things were done that way, so I try to copy the way the old masters were doing it.
This is all the joys of being a female woodworker.
[Electric saw whirring] ♪ Narrator: After the pieces are cut, Natalie hollows out the soundbox, which amplifies the sound made by the strings.
She will often spend several weeks getting it just right.
Natalie: I'm just finishing the sides of the soundbox.
So the idea is to make them completely flat.
When I get to the fine bits, I start using hand tools quite a lot 'cause there's more control.
Narrator: The soundbox needs to be just the right thickness.
Too thick, it produces a dull sound; too thin, the wood will break, and then she'll have to start all over.
Natalie: It'’’s not a kind of a science, you know.
It's just trial and error.
That's it.
[Different tapping sounds] Can you hear it here?
It's much louder and kind of brighter.
This dull section, I need to kind of improve it.
Narrator: Next, Natalie shapes the pillar.
This is the spine of the harp, the piece that helps support it.
[Filing] In this case, she makes the pillar in the shape of the Salmon of Knowledge-- a creature from a beloved Irish legend.
[Continues filing] Here we have a head and the lip and the eyes.
And because it'’’s so smart, instead of the tail, it has the second head.
[Giggling] Narrator: Carving the salmon into the harp'’’s pillar is a nod to Irish history and a practical matter, too.
Natalie: Everyone thinks it's a decorative part, but actually, it has a function.
It prevents the pillar from warping.
Narrator: When all the pieces of the harp are made, Natalie fits them together.
Natalie: No glue at all.
[Tapping] You don't really need any because the joints are so tight.
So, it's like the magic of medieval engineering.
[Laughing] Narrator: Natalie is down to the final steps.
First, she adds designs into the wood, then paints and varnishes it.
Last, Natalie adds the strings.
Some larger harps have as many as 36 of them.
She tunes each string to make sure it has the right amount of tension to help create the harp'’’s lush, lyrical sound.
[Plucking strings] [Playing scale] Natalie: My favorite part is to play its first tune.
So, when you play the first tune when the harp is in tune and you can hear its voice, this is my... Yeah.
Then you feel, yeah.
[Giggles] Narrator: Every time Natalie finishes a new harp, she finds herself falling in love all over again.
You don't want to give it away.
Usually it's for a customer and you're like, "No, I don't want to part with it.
I want to play it."
[Harp music continues] ♪ Narrator: Despite her roots as a historian, Natalie has found her true passion--making harps.
♪ Natalie: It's a labor of love.
I really--I love my job.
So, every time I come here, I just like, "Oh, I'm so lucky."
[Laughing] The person who was going to spend all her life in academia suddenly started doing this and couldn't stop.
[Giggling] 17 years later, I'm still at it.
Narrator: Further north, in a scenic corner of County Galway is Connemara, an area known for its "savage beauty" and not too far from the remains of the 12th-century Castle Kirk.
With its soaring peaks and sprawling bogs, Connemara's rugged landscape has long been a source of inspiration.
My name is Joe Hogan.
I'm a basket maker, and I live in Connemara, Ireland.
Narrator: For Joe and his wife Dolores, it was their love of this land that first drew them here more than 40 years ago.
Well, I think the landscape, for me, speaks for itself.
It's a very beautiful place.
We were both interested in gardening and plants and growing some of our own food.
Narrator: They also grow and harvest the willow Joe needs to create artistic and traditional Irish baskets.
Joe: I was drawn to basket making because of the willow, by a desire to forge a slightly deeper connection with the natural world.
Narrator: Rows of willow line Joe's driveway, where they dry and harden for up to a year.
[Rustling] Today, Joe will use some of his willow to make a traditional basket known as a skib.
Skibs were used in the early 1800s to drain and serve boiled potatoes.
Certainly in the 1800s, potatoes, even though they're not a native plant, they were the main diet of the people.
Narrator: Joe relies on many of the same techniques that basket makers have used for centuries.
He uses the thickest and stiffest pieces of willow to form the grid at the base of his skib.
Joe: So, this is the kind of grid-type opening.
Narrator: Then Joe carefully begins to wrap the base with supple pieces of willow.
Unlike traditional basket makers, he uses different shades of willow to add a splash of color.
Joe: It kind of started by accident 30 years ago, because I used to have a very pliable yellow rod, and I found that people liked it.
It's quite an instinctual process.
I don't draw the basket beforehand or anything like that.
Announcer: Next, Joe adds long rods that will help shape the walls of the skib.
Once he turns the rods upright, a simple hoop will keep them in place.
Joe: this is called a wrapping iron.
It's a basket maker's hammer.
And I now need to use it just to ensure that all my uprights are in tight and close so that there won't be any air holes between the sides and the base.
[Tapping] Narrator: But his greatest tools are his hands.
Making a skib can take up to 3 hours.
Joe also weaves bigger and more complex designs that take days to finish.
He's learned to pace himself.
Joe: There's a proverb in Irish "Suí I gearr ná seasamh fhada."
"It's better to be sitting for a short time than standing for a long time."
Narrator: Over the years, Joe has made thousands of baskets and sculptures.
He also turns to classic Irish designs, like the lobster pot and the donkey creel.
Joe: Some of the weaves are unique to this country, and I find them really useful weaves in the work I do now.
Narrator: At last, the skib is almost done.
One of the final steps is to add a border and the finishing touches.
Joe: Trimming off the end pieces, and hope to use them in another project.
[Cutters snipping] I get very absorbed in the process when I'm making baskets.
So, to say that you don't feel the day going by, it would be an understatement, to be honest.
This is it, the skib, the basket which was used for straining and then serving potatoes.
Narrator: For Joe, his love of nature led him to basket weaving and finding ways of bending nature's raw materials to his artistic vision.
Joe: I just think of it as being absorbed in what I'm doing.
You are going to have to spend long hours at it.
You have to love this kind of work.
Narrator: In the middle of Ireland's heartlands lies one of its oldest counties--Tipperary.
Here, the mighty Rock of Cashel rises above lush green fields... a striking reminder of Ireland's medieval past.
Woman: We are seen as being a traditional part of Ireland.
When you're visiting Tipperary, you feel everything is moving slower because it actually is.
My name is Ailbhe Gerrard.
I'm a beekeeper and a beeswax candle maker in Tipperary, Ireland.
Narrator: Ailbhe grew up in Tipperary, then moved away to college to study sustainability.
She worked in Dublin and abroad until a conference on climate change led her back home.
Ailbhe: I was absolutely astounded by what I learned, and I said to myself, "I need to get into agriculture, "because agriculture is the key to climate change and biodiversity loss."
Narrator: Within a year, she bought a farm next to her parents with the goal of producing organic food and sustainable products.
[Hissing] [Buzzing] Narrator: Before long, she discovered the wonder of bees.
Ailbhe: I started beekeeping because as an organic farmer I was really interested in insects and what they needed, because insects are in many ways the basis of the food chain.
And then realized that wax, beeswax, is an incredible, natural, extraordinary substance.
So I started making things from it.
Narrator: In medieval Ireland, beeswax was considered a luxury item used for candles, seals, and adhesives.
Honey was the only available sweetener, so most families kept their own hives to ensure a steady supply.
Ailbhe has around 15 beehives on her farm.
Once the bees are done with them, she collects the honeycomb frames.
[Scraping] Ailbhe: Once we extract the honey from it, we're left with the empty comb, so we can melt that down, and then you end up with a block of beeswax like this.
It looks almost like cheese.
You can see.
It looks like you want to eat it, doesn't it?
Narrator: The color of the beeswax reflects what the bees have been eating.
Ailbhe: These bees have probably been feasting on summer flowers and multi floral, so this is a particularly bright color, so I like making candles out of this one.
Narrator: Today, Ailbhe's making birthday candles.
She prepares each wick of braided cotton by tying a metal nut to the end to keep it straight as she dips it into the melted beeswax.
[Birds chirping] The key is keeping the liquid wax at just the right temperature, no more than 158 degrees.
Ailbhe: Slowly, slowly, each pair goes in.
We keep on going, section after section, dip, dip, dip.
Making candles is like baking.
If something is off, then you have a disaster.
In the beginning, it feels like you're not getting anywhere, but as time goes on and you do repeated dips, then you start seeing the layers building up.
Narrator: Birthday candles need only 5 or 6 dips.
Dinner candles can take 20 or more.
Ailbhe: The whole process, it takes usually about 8 hours start to finish.
Narrator: The result... beautiful beeswax candles hand-made only steps from the hive.
Ailbhe: Most candles aren't beeswax.
Most candles aren't traditionally hand-dipped.
It's just, like, lovely to see that process through from beginning to end and then have happy customers.
It feels like such a privilege to be working on the land with the help of the bees.
Narrator: And savoring a bit of leftover honey.
Mmm!
That is one of my best honeys.
Thank you, bees.
[Exhaling air] Narrator: Thousands of years ago, people settled in the county of Sligo for its abundance of shellfish.
In Gaelic, Sligo or "Sligeach" means "shelly place."
With its inlets, cold, wet climate, and clean water, Sligo Bay provides a perfect environment for oysters to thrive.
Man: I'm Glenn Hunter.
I'm an oyster farmer from Sligo, Ireland.
Narrator: Glenn Hunter's been farming on Sligo Bay most of his life.
Glenn: Me dad and a few of the guys got together and started clam farming back in the late eighties.
We grew clams for 20 years, and we went over to growing oysters.
Narrator: Glenn's wife Aisling also grew up in Sligo.
She moved away for 15 years, then met Glenn two days after she returned home.
Aisling: He said he was an oyster farmer, and I was like, "Sligo has oysters and farms?"
And then we were dating a few weeks, and then once I seen the farm I was like, "This is incredible."
I fell in love straight away with an oyster farmer and oysters.
Ha ha!
Are we good to go?
Narrator: Each day, Glenn and his team head to the shore when the tide is out to tend to the farm.
[Boat chugging] Growing an oyster is a labor-intensive process that takes about 3 years.
Glenn: I like getting out in the fresh air and the sea breeze and just big open space.
And you never know what you're going to see.
Every day is different down in the oyster farm.
The oysters are grown in oyster bags on top of oyster trestles which keeps the oysters up off the ground.
And it stops the oysters getting suffocated in the sand, keeps them up off the crabs, and it keeps them up where the most food is in the water, which is up higher.
[Oysters rattling] Today, we're down here turning the oyster bags.
Narrator: Oysters grow between March and October.
Glenn's team turns the bags monthly to break off new shell growth, which helps strengthen and shape them.
[Rattling] The goal is a deep, cup-shaped oyster.
The deeper the cup, the better the meat.
Glenn: Here we have the lovely teardrop shape and the deep cup as you can see.
Narrator: Each bag of oysters is brought in once a year and graded according to weight and size.
They haul in up to 600 bags at a time, 50,000 bags in all.
Glenn: Keeps you in shape, all right.
I don't know any better.
Ha ha ha!
Narrator: The largest oysters are shipped to restaurants around the world.
People abroad have been enjoying oysters from Sligo since the 1800s, when the first farm here sent oysters straight to London.
Aisling: So, Harrod's was eating oysters, and all these amazing restaurants were eating Sligo oysters.
So, there was a really strong history.
Narrator: An appreciation developed abroad, but it took a while for oysters to catch on in Ireland.
Definitely a growing trend, I think here.
So, people are eating them more and more.
Once they know about them and hear about how they're farmed and the sustainable practices, they all want to taste them.
Oysters clean your bays.
They're really good for the environment.
They're really good for you.
Narrator: When you're ready to eat, you'll need a sharp eye, a gentle touch, and a good oyster knife.
Glenn: You just go in here on the side of the oyster... and you shake the knife a little bit.
Once you get the knife in, you twist it... [Shell cracks] get the knife, and you slide it on the bottom of the shell.
Just flip it over, take off a bit of the salt, and fire it back.
♪ Aisling: An oyster is like kissing the sea on the lips, so it is like literally tasting the sea.
And they're just so fresh.
There's nothin like tasting fresh oysters from where they're from, you know?
It's really nice.
Narrator: A love of oysters and Sligo they hope to pass on to their daughter Kelly.
Aisling: Kelly loves being out and about with us.
I hope she travels the world and she can tell everyone about how amazing our oysters are and whatever she wants to do.
Glenn: And the world is her oyster.
Aisling: Yeah!
Narrator: Growing up, Irish poet William Butler Yeats spent his summers in Sligo.
Later, he wrote about this coastal county with a boy's sense of wonder.
Woman: "A moon worn as if it had been a shell, "washed by time's waters as they rose and fell about the stars and broke in days and years."
I'm Martina Hamilton.
I'm a jewelry designer from Sligo, Ireland.
Narrator: For local artisan Martina Hamilton, the poetry of Yeats and the Atlantic coastline inspire her jewelry collections.
Martina: I like to think that I engender a sense of place into the jewelry I make.
There's absolutely no shortage of inspiration from finding shells on the beach, and sometimes a simple thing like just looking down at the ground and noticing a shell that's turned a particular way starts the creative process.
And I like to kind of catch that experience if I can in a piece of metal.
Narrator: From her studio in town, Martina and her team of master goldsmiths are crafting a pendant and pearl necklace inspired by the oysters of Sligo.
[Machinery buzzing] She starts by carefully measuring and cutting two circular discs from a thin sheet of sterling silver.
[Sawing] When you're working in silver, of course, you're in a very small world, and once you get into that small world, everything is down to the millimeters.
[Tap] Narrator: Most of the tools used in the workshop have been around for centuries.
[Tapping] A doming punch helps Martina give the discs a gentle curve, then she painstakingly drills a tiny hole for a needle-thin saw.
Martina: A very steady hand is required and patience.
You have to just focus very closely on one thing at a time, which is the beauty of it, really, as well.
When you're concentrating on making something, everything else is gone.
[Flame pops] Narrator: Martina's brother- in-law handles the soldering, applying heat evenly to attach the silver discs.
Martina: Every little detail has to be calculated.
You want something to be light and comfortable to wear, but at the same time, it has to be physically strong.
So, there's a lot of knowing in it.
[Buzzing] And then the outer shape is textured as a shell might be.
[Buzzing] [Filing] Narrator: Once the metal is filed and polished, Martina attaches the pearl.
Martina: I wanted to do something that was a bit asymmetrical, and I wanted to have the feeling of that lovely soft center of the shell on the inside and make a little cozy, safe space for the pearl.
Narrator: From the spark of an idea to a finished piece... inspired by the seas of Sligo.
Martina: The loveliest thing is, we've made something that's classic that lasts a lifetime.
It continues to inspire me.
I hope that I succeed at least sometimes in conjuring up this very special place that is Sligo.
It's home.
Narrator: In southwest Ireland, the country's largest county is bounded by over 1,500 miles of coastline.
Here, the pristine waters of County Cork offer up an abundant gift--seaweed.
For generations, it was harvested as a source of fertilizer and food.
When potato crops failed during the great famine in the 1800s, seaweed became a lifeline for survival.
Woman: Seaweed is nothing short of a miracle.
It's great for healing, it's great for cleansing your body.
There's so much nutrition in it.
I'm Claire O'Sullivan.
I work with seaweed in County Cork, Ireland.
Narrator: At low tide, Claire and her partner Eli head out to collect seaweed by hand, the same way it's been harvested for generations.
Claire: I really do feel a connection to the people who've gone before me, you know.
It's such a simple process-- going down, basket, scissors.
You just have the coastline, the water, and you're doing it the very same way as my nanny, my great-grandmother, and God knows how many more before them.
[Water splashing] They were able to take care of the seaweed and not overdo it.
You just take a little bit here and a little bit there, so it was always there for the generations after them.
There's an old Irish saying.
It was in pre-famine times.
And "Number 1 was the spuds, "number 2 was the children, and number 3 was the seaweed."
That's how important the seaweed was.
Narrator: Claire hopes to restore seaweed to its rightful place of honor by using it in everything she makes... from pestos to body scrubs.
Today, she's making seaweed-infused facial oil.
Claire: So, this is lovely dry seaweed now.
We have to make sure it's good and dry to prevent any molds, any bacteria from growing in it and just make sure you get the most beautiful facial oil.
Narrator: Claire covers the seaweed with sweet almond oil.
Claire: It allows all the trace minerals, trace elements that are in the seaweed to be absorbed into the oil.
You're getting all the nourishment and all the health of the seaweed.
Narrator: After 6 weeks, Claire strains the oil and adds her own special blend of essential oils: jojoba for nourishment... geranium to balance the complexion... lavender oil for relaxation... and finally, bergamot to make the skin glow.
Claire: I actually think what makes our products unique are how simple they are.
We use the most natural of ingredients, and that's why I feel they're wonderful.
That is handmade, hand-labeled, seaweed-infused facial oil.
[Water splashing] I feel so proud of my products.
I feel so proud that I'm using Irish seaweed, hand-harvested.
We get messages from people saying they love them, and you're like, "You know, I'm doing something right.
I think I'm going in the right direction."
So, it makes you feel, job well done.
Narrator: It's hard to think of Ireland without picturing dramatic cliffs carved by the roaring Atlantic that form the western border of County Clare.
This rugged landscape of limestone and shale is part of a geographic region known as the Burren, or "an bhoireann"-- Irish for "place of stone."
The peaty soil above this rocky terrain is usually damp from fog and rain.
The land might not be ideal for conventional farming, but it's great for goats and goat cheese.
My name is Siobhan Ni Gháirbhith.
I'm a cheesemaker from County Clare in Ireland.
Narrator: 8 miles from the Atlantic coast and south of the Burren, Siobhan runs a goat farm on land that's been in her family for generations.
Siobhan: Our farm--it actually starts with the goats.
[Bleating] First thing in the morning, we bring the goats in, and we milk them in the morning time and we feed them.
It's all about what the goats eat to give us the good-quality milk.
The land itself, I would say, is quite wild and natural.
We have lovely natural vegetation like buttercups and clover and ferns growing in the grass that the goats love to eat.
The land is very flavorsome is what I would say.
Narrator: The flavors of the land enhance the milk-- saltiness from the nearby sea... earthiness from the peaty soil... a true taste of County Clare.
Siobhan reconnected with this land more than 20 years ago when she bought the goat cheese business.
My parents were delighted when one of us showed interest in farming because we had all gone on in different careers.
Narrator: Today, Siobhan passes along her love of the farm and Irish cheese to her daughter Luisne.
They're making goat cheese by hand, the same way it's been made all along.
It all starts with fresh milk that goes straight to the cheese house, where the milk stands for 24 hours, long enough for it to separate.
Siobhan: At this stage, we add the starter to the milk.
This is to break down the milk so that the following day, we will have curds and whey.
So, what we're doing now is, we're draining off the curd.
So, we've got the whey on top, and then we've got the lovely fresh curd.
And you should be very gentle.
The more gentle you are with the curds, the more smoother and creamier cheese that you get.
Narrator: After they drain off the whey, the curds are ladled by hand into molds where they settle overnight.
Siobhan: We have the natural saltiness in the land, in the grass, so we don't have to add that much salt, which is great because the less salt you add, the more the natural flavors come out in the cheese.
Narrator: In just a week, the family's goat milk is transformed into logs of fresh cheese.
Siobhan: This is the original cheese that we made when we started over 23 years ago.
It's used by chefs.
They do fantastic things with it, whether they bake it or just serve it slightly warmed with a salad-- Pizza.
all sorts of creative things.
Yes, they use it on pizza.
My daughter likes pizza.
Narrator: Some of the cheese gets one final treatment-- a thin layer of "ash" is rolled on.
Made from burnt vegetables, this coating helps bring out the flavor, despite how it looks.
Siobhan: So, when you actually coat it in this food-grade charcoal, it locks in the moisture for longer, and it just gives a nice contrast flavor.
Ha ha ha ha!
You have to have a bit of fun!
Ha ha ha ha!
I very much love the job that I do.
I don't even see it as a job.
It's a way of living.
It's very much about working with what nature gives you.
You're at the mercy of Mother Nature and what the animals decide to do on any given day.
As I grew up, I became more aware of how important it was to protect the land that we're lucky to have here-- that it's not just for my generation, but for future generations, for my children, my grandchildren.
[Bleating] Narrator: In Ireland, it's the connection between the people, their land, and their traditions that drives these artisans to dig deeper and dream bigger, as they share the beauty of this Emerald Isle with the world.
Claire: I really do feel a connection to the people who've gone before me, and I feel that's very special.
Miriam: We're really passionate about sustaining that heritage.
You're sending that kind of love and passion all over the world.
Narrator: Their passion has led to the creation of some modern masterworks, pieces that are both personal expressions and portals to the past... Celtic visions made with love.
♪ ♪
Ireland Made With Love Preview
Video has Closed Captions
Preview: Special | 30s | Explore Irish craftmanship and the skill, love and pride that go into legendary products. (30s)
Providing Support for PBS.org
Learn Moreabout PBS online sponsorshipSupport for PBS provided by: